Beyond Forms and Checklists: How IoT Enhances Frontline Operations
- PinPoint
- Sep 17, 2024
- 5 min read
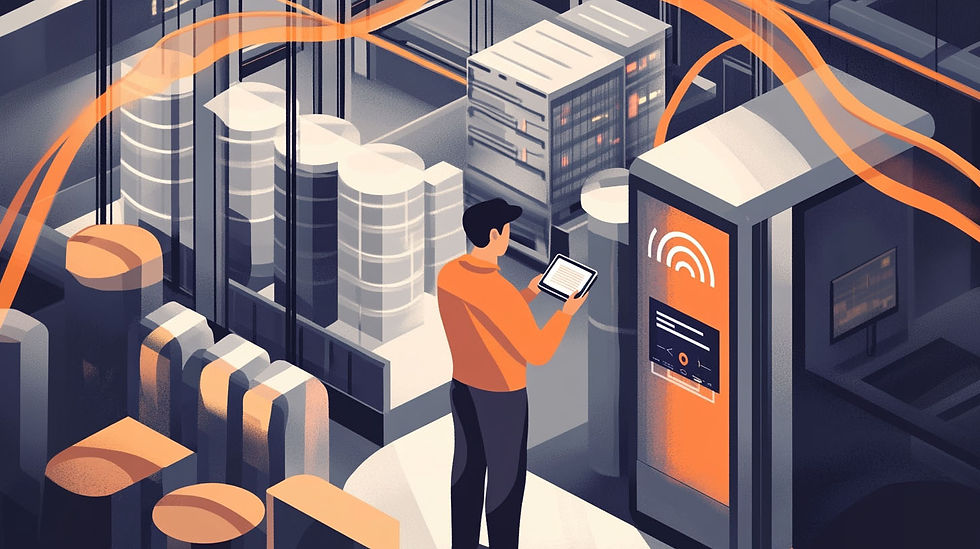
Relying solely on forms and checklists for frontline operations is no longer enough. While these tools help maintain order and accountability, the advent of the Internet of Things (IoT) is revolutionizing how frontline workers interact with their environments, equipment, and tasks. IoT, through connected devices and real-time data, offers far-reaching benefits that go beyond traditional methods. This article will explore how IoT can enhance frontline operations, streamline processes, and drive better results in real-time.
The Limitations of Traditional Methods
Forms and checklists are standard tools in many frontline operations, used to track tasks, monitor progress, and ensure compliance. While useful, they have limitations.
Manual Data Entry: Workers often need to input information manually, which is time-consuming and prone to human error.
Delayed Response: Without real-time data, responding to potential problems or incidents may take longer, risking delays in resolving critical issues.
Limited Scope: Traditional methods typically rely on what a worker observes and records. Critical issues can go unnoticed until they're too big to ignore.
What is IoT and How Does it Work in Frontline Operations?
The Internet of Things (IoT) refers to the network of physical devices embedded with sensors, software, and connectivity to exchange data with other systems and devices. In frontline operations, IoT devices can be attached to machinery, tools, and other critical equipment to gather and transmit real-time data about performance, safety, and maintenance.
This technology opens a wide range of possibilities for better resource management, real-time monitoring, and proactive decision-making, far beyond what traditional forms and checklists can offer.
Real-Time Data Collection and Analysis
One of the most significant advantages IoT offers is real-time data collection. Sensors and connected devices allow frontline workers to monitor conditions continuously, providing valuable information instantly.
For example, in a factory setting, IoT sensors attached to machines can monitor temperatures, vibrations, and pressure levels. If any of these metrics deviate from the norm, the system can automatically alert the relevant personnel, enabling them to take immediate corrective action. In addition to preventing costly breakdowns, IoT also minimizes the chances of workers entering unsafe environments.
The PinPoint Workforce app excels in this area by integrating IoT capabilities with traditional forms and checklists. By supplementing manual checks with real-time sensor data, PinPoint allows frontline workers to make more informed decisions faster, ensuring safety, quality, and efficiency.
PinPoint’s Native IoT Solutions
PinPoint Workforce natively supports several IoT technologies, including geofencing, beacons, QR codes, and barcodes. These features allow organizations to instantly integrate IoT solutions into their workflows. For example, geofencing can be used to trigger safety procedures when a worker enters a restricted area, while QR codes can provide immediate access to equipment maintenance histories or operational protocols. Beacons can also notify workers of critical updates as they move throughout the facility.
These tools provide an efficient, instant way to enhance workflows without the need for additional infrastructure. However, for more advanced IoT implementations, such as integrating wearable devices or monitoring machinery in real-time, PinPoint supports custom integrations through its API. This allows for deeper IoT adoption, such as integrating data from wearable devices that track worker vitals or machine monitors that flag potential malfunctions. PinPoint’s team collaborates closely with organizations to ensure these custom solutions are tailored to meet their unique needs, ensuring a seamless integration of IoT into their workflows.
Predictive Maintenance for Greater Efficiency
Preventive maintenance is another significant area where IoT shines. Traditionally, equipment is serviced on a set schedule, regardless of its actual condition. This often results in unnecessary maintenance or, conversely, equipment failures between maintenance cycles.
IoT enhances this process by enabling predictive maintenance. IoT sensors continuously monitor equipment and send alerts when maintenance is required. This is particularly beneficial for frontline operations where equipment downtime can cause delays or safety issues.
For instance, imagine IoT sensors installed on forklifts, monitoring their usage and performance in real time. When certain performance indicators suggest that the forklift needs maintenance, a task can be automatically generated in the PinPoint Workforce app, ensuring timely repairs and avoiding costly breakdowns.
With predictive maintenance powered by IoT, companies can reduce downtime, minimize costs, and ensure equipment is always operating at optimal efficiency.
Enhancing Safety with IoT
Frontline operations can be hazardous, and safety is a primary concern for both employees and employers. IoT is playing an increasingly critical role in enhancing safety measures by offering real-time monitoring and alerts that forms and checklists simply cannot provide on their own.
Wearable IoT devices, such as smart helmets or safety vests, can monitor a worker's vitals and environmental conditions. If a worker's heart rate spikes or the temperature becomes dangerously high, the device can send an alert to supervisors or an emergency response team. This real-time feedback ensures that potential dangers are addressed before they escalate into serious incidents.
PinPoint Workforce can incorporate IoT-generated safety alerts directly into task assignments and corrective actions. If a sensor detects a safety breach, PinPoint can automatically notify the relevant team members and assign them tasks, such as evacuating the area or investigating the issue.
Improving Asset Tracking and Inventory Management
Managing assets and inventory can be challenging, especially in large-scale operations. IoT can simplify this process by providing real-time tracking and visibility into the location and condition of assets. This improves operational efficiency and reduces the chances of loss or theft.
For example, IoT-enabled RFID tags or Ultra-Wideband (UWB) devices can be placed on critical tools or equipment, providing a digital record of their movement. UWB devices offer more precise tracking than traditional RFID tags, making them ideal for tracking high-value assets in large or complex environments. Workers can easily scan these items with their mobile devices, which update the system in real time. This level of visibility ensures that tools are always where they need to be and are in the right condition for the task at hand.
By integrating this technology with PinPoint Workforce, managers can assign tasks based on the real-time location of equipment, ensuring smooth and efficient operations.
The Role of IoT in Spaced Learning
IoT also plays an unexpected role in training, particularly in spaced learning programs. By integrating IoT devices with training software like PinPoint Workforce, organizations can deliver training at critical points. For example, when a machine indicates wear and tear, workers can receive a timely training reminder on machine maintenance, helping them retain important information when it's most relevant.
PinPoint Workforce excels at using IoT data to tailor spaced learning programs, ensuring that workers receive training updates based on real-time situations, enhancing both retention and effectiveness.
Streamlining Regulatory Compliance and Reporting
Compliance is an integral part of many frontline operations, whether it's adhering to safety regulations, environmental standards, or industry-specific guidelines. Traditionally, workers would fill out forms or checklists to ensure compliance. However, the manual nature of this process can lead to errors or inconsistencies.
IoT automates much of the compliance process by collecting real-time data and ensuring that every aspect of an operation is monitored. Sensors can track and log safety conditions, such as air quality or temperature levels, ensuring that the workplace meets all regulatory requirements.
PinPoint Workforce integrates IoT data directly into its reporting tools. If any compliance metrics are not met, the system can automatically generate a report and assign corrective actions to the appropriate team members, ensuring swift resolution and accountability.
Conclusion
IoT is not just a buzzword; it's transforming the way frontline operations are managed, enhancing productivity, safety, and efficiency. By integrating IoT with digital platforms like PinPoint Workforce, organizations can move beyond the limitations of traditional forms and checklists to create a more connected, responsive, and data-driven workforce.
With the native support of geofencing, beacons, QR codes, and barcodes, PinPoint Workforce provides immediate IoT solutions for frontline operations. For more advanced IoT implementations, such as wearables or UWB tracking, PinPoint’s API and collaborative approach ensure that your IoT systems are tailored perfectly to your organization's needs.
Ready to integrate IoT into your frontline operations?
Contact us at info@pinpointworkforce.com to learn how PinPoint Workforce can support your transition to IoT-powered operations and help drive long-term success.
Comments